Pre-Engineered Buildings (PEBs): Revolutionizing Construction

Pre-Engineered Buildings, or PEBs, are a game-changer in the world of construction. These innovative structures are designed and manufactured off-site, allowing for unparalleled efficiency and cost-effectiveness in building projects of all sizes. Here’s a brief overview of PEBs and how they’re made:
What Are Pre-Engineered Buildings (PEBs)?
Pre-Engineered Buildings (PEBs) are custom-engineered steel structures that are manufactured in a controlled environment and then transported to the construction site for assembly. They are designed to meet specific project requirements, making them highly versatile and suitable for various applications, including warehouses, industrial facilities, commercial buildings, and more.
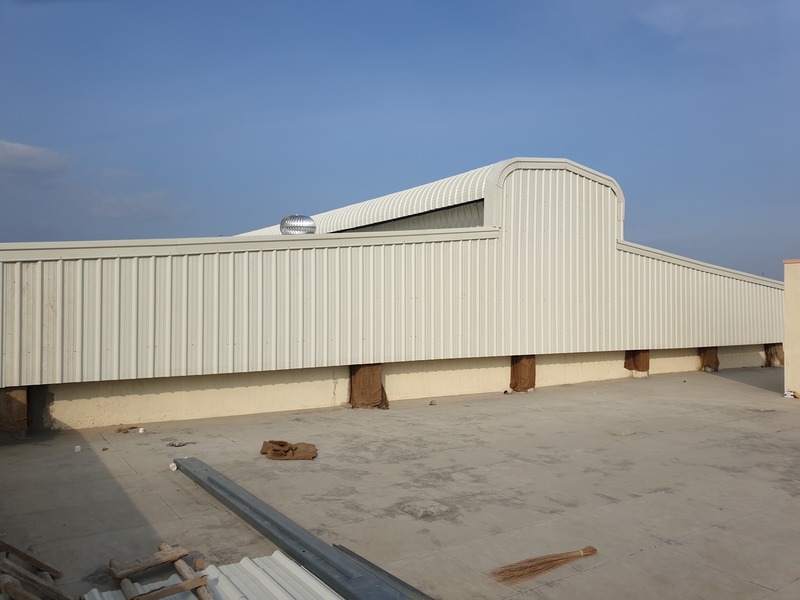
The PEB Manufacturing Process:
Design and Engineering: The PEB process begins with meticulous design and engineering. Architects and engineers work together to create a structure tailored to the client’s needs, taking into account factors such as size, function, local weather conditions, and seismic considerations.
Material Selection: High-quality steel is the primary material used in PEBs due to its durability, strength, and versatility. Steel components are typically sourced from reputable suppliers.
Fabrication: Once the design is finalized, the steel components are fabricated in a factory-controlled environment. This involves cutting, shaping, welding, and painting the steel to precise specifications. The use of computer-aided design (CAD) and computer-aided manufacturing (CAM) technologies ensures accuracy and consistency.
Quality Control: PEB manufacturers employ stringent quality control measures to ensure that all components meet industry standards and project-specific requirements. This includes rigorous testing and inspections throughout the manufacturing process.
Packaging and Transport: After fabrication and quality control checks, the steel components are carefully packaged and transported to the construction site. This reduces material wastage and minimizes on-site construction time.
Assembly: At the construction site, PEBs are assembled using bolted connections. This assembly process is significantly faster than traditional construction methods, saving time and labor costs.
Advantages of PEBs:
- Cost-Effective: PEBs offer cost savings in terms of materials, labor, and construction time.
- Customization: They can be tailored to meet specific design and functional requirements.
- Speed of Construction: PEBs are quick to assemble, reducing project timelines.
- Durability: Steel structures are known for their strength and longevity.
- Energy Efficiency: PEBs can be designed with energy-efficient features, reducing long-term operational costs.
- Sustainability: Steel is a recyclable material, making PEBs an environmentally friendly choice.
In summary, Pre-Engineered Buildings (PEBs) represent a cutting-edge approach to construction, combining efficient design, high-quality materials, and controlled manufacturing to deliver cost-effective, durable, and customizable structures. Whether for industrial, commercial, or institutional use, PEBs are revolutionizing the way buildings are constructed. Explore the possibilities today!